- Technologies
- Substrate & filter technologies
Substrates and filter technologies
Silicon Carbide diesel particulate filter
The primary function of a Diesel Particulate Filter (DPF) is to trap and reduce particulate matter mass (PM) in the diesel exhaust by > 95 % and the particulate number (PN) by > 99 % at the cost of minimal possible back pressure. At the same time the DPF needs to be able to withstand high thermal stress generated by high soot load levels combined with active regeneration.
The new Dinex Silicon Carbide DPF CHP-SiC is a robust substrate technology with moderate back pressure under high soot and ash loads. It is available at a porosity level of 54-58% (CHP-SiC-5 and CHP-SiC-K05) for catalyzed DPF applications and at a high porosity level up to 65% to accommodate high wash coat loadings, typical for SCR on DPF applications.The catalytic coating for catalyzed DPF applications is designed for a low impact on back pressure and to work under passive as well as under active regeneration strategies.
The high porous Silicon Carbide CHP-SiC is based on a reaction forming process of metallic silicon and graphite which form in-situ the SiC skeleton in the thermal oven process. The final porous structure is built up by fine SiC crystals, which build a three-dimensional network with a high pore volume.
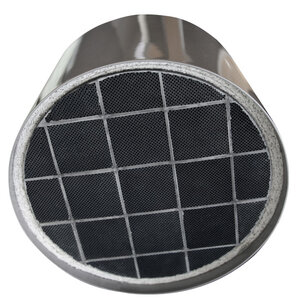
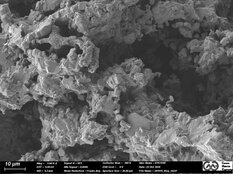
CHP-SiC-K05
Metallic Substrates
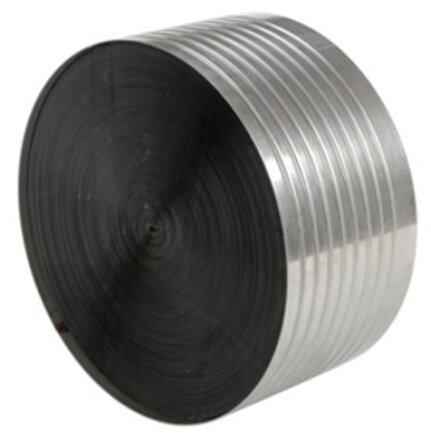
Metallic Substrates with a grooved structure
The substrates feature a grooved lock mechanism that provides the necessary mechanical resistance while improving flow dynamics. Made with high quality stainless steel, they are lightweight and easy to integrate into the exhaust system. The use of thin foils allows a fast heat at low thermal inertia up and the grooved structure improves the mass transfer rates while maintaining low backpressure. For applications where high temperatures are expected - like CNG/LNG ATS systems - brazing of the substrates is done to add additional mechanical durability.
Substrates are available in the cell densities 120, 200, 350 and 500 cpsi.
Dinex substrate portfolio is designed for heavy-duty applications running on both diesel and CNG/LNG.
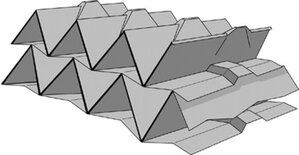
Metallic filters (POC)
The primary function of a metallic filter based primary oxidation catalyst (POC) is to reduce the particulate matter mass (PM) by at least 40 – 50% and find application in some older generation emissions regulations like EU IV and some current and upcoming off-road regulations in developing countries like India.
Dinex POC ® is an open filter substrate, developed to trap particulate matter in light-duty and heavy-duty diesel vehicles and have special X layer structure. The substrates are characterised by having high mechanical durability, excellent flow distribution and maintenance free flow through construction. Coated with specific wash coat, they are made of a 100 % stainless steel structure.
The substrates are available in 330 cpsi configuration with standard length of 152 mm.
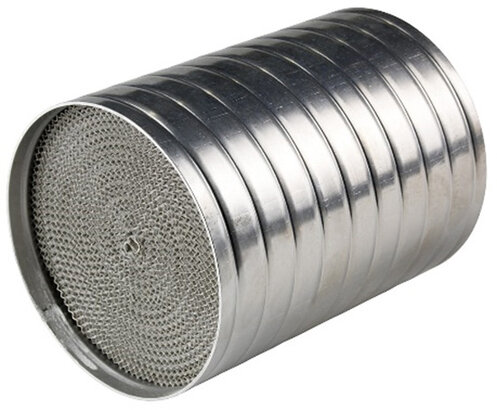
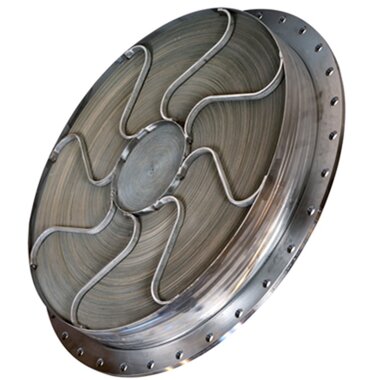
Metallic substrates with straight channels and large dimensions
For large dimensions also rolled and pinned substrates, as well as pulse welded or brazed substrates with straight channels, are available. Round products up to a diameter of 2.5 meters are part of the Dinex product portfolio as well as standard square box designs. Typical applications for these types of substrates are catalytic converters for large engines like TWC (three way catalyst), MOC (methane oxidation catalyst) DOC (diesel oxidation catalyst), or SCR (Selective Catalytic Reduction).
Substrates are available in cell densities 120, 200, 350 and 500 cpsi.