- News and Events
- News
- The science behind clean air
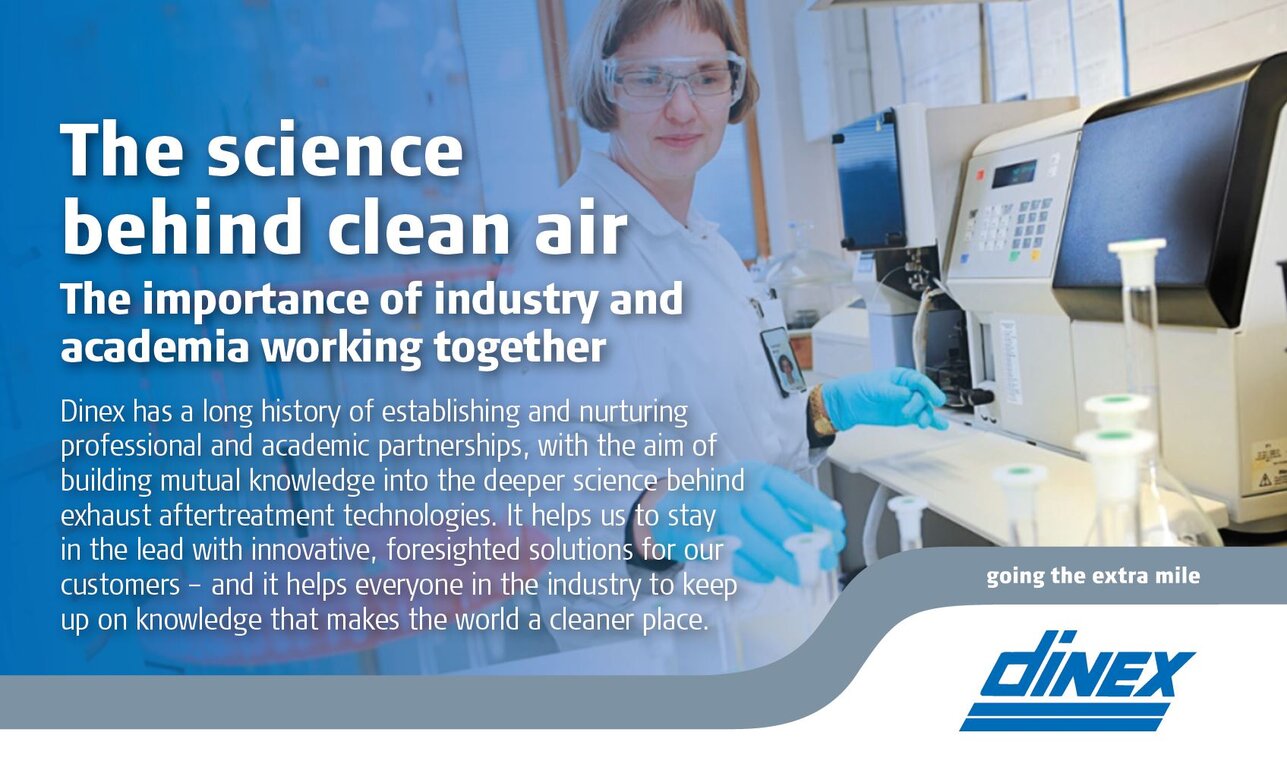
Aftertreatment catalysts are complex products that bring great environmental benefits by keeping tailpipe emissions under control. But with the natural evolution and constant improvements internal combustion engines are subject to, aftertreatment systems and catalysts always face changing conditions that they must in order to keep performance to the max!
Insight into the various mechanisms and phenomena behind the catalyst behavior is key information that directly connects into the next generation of emission control products. Together with our partners, we dive down to the molecular level and gain knowledge which we jointly publish for the benefit of the whole industry. In this article we take you through a short journey through the world of catalysts and how our scientific partnerships produce valuable knowledge.
Understanding Deactivation
One of the topics we have been looking into are the deactivation mechanisms for Platinum (Pt) on common material carriers. Awareness of how different types of poisons commonly found in fuel and engine lubrication oils affect and react with the active phase of the catalyst helps us formulate chemical coatings that take these effects into consideration when screening for new materials.
This knowledge also helps create regeneration strategies and build up tolerance against poisoning though various design features such as coating construction and architecture. In a recently published paper by one of our academic partners we investigated the surface poison distribution of a Platinum based catalyst sample by Scanning Transmission Electron Microscopy/Energy-Dispersive X-ray Spectroscopy (STEM-EDS). Fig 1 shows the different levels of elements identified and how they distribute in a particular area of the sample.
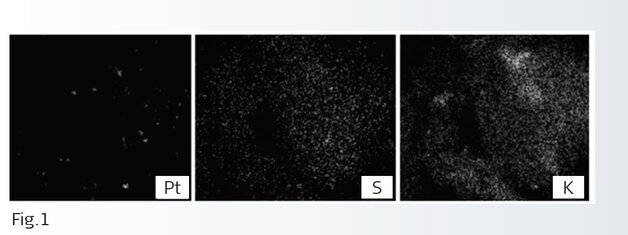
Together with our research partners we had the opportunity to characterize these processes in detail broadening our knowledge base and helping us find solutions against poisoning on key products such as Diesel Oxidation catalysts (DOC) while contributing to academic advancement in the area of catalysis.
Finding Solutions
Compressed (CNG) and Liquified Natural Gas (LNG) fuels and engine technologies are key areas of development and applications, both for on-road markets and other applications, which are also of interest for Dinex. This is well evidenced by the recently published paper of another partner. The work was focused on finding a way to regenerate (recover) the performance of a Methane Oxidation Catalyst (MOC) under the typical lean conditions of an engine running on LNG – thus keeping the catalytic efficiency at an all time high level.
The investigation revealed that is possible to regenerate/recover the MOC activity by performing a regeneration cycle and by combining this with an upstream trap designed to prevent the bulk of the poisons from reaching the MOC. Figure 2 shows the typical performance of the MOC fresh and how it increases with temperature.
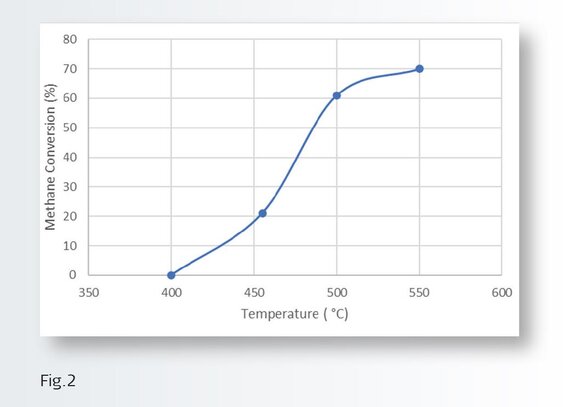
Through cooperation and partnership with academia and research institutes Dinex complements and enriches the knowledge in the field of catalyst aftertreatments while staying actively involved and connected to its own development agenda. This synergetic approach has been the key to building partnerships that have lasted decades.
Interested in cooperating with Dinex in the field of emission control catalyst?
Reach out to Dr Thomas Wolff and Dr Andreina Moreno for more information.
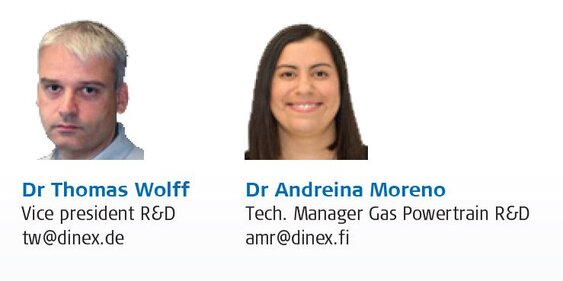
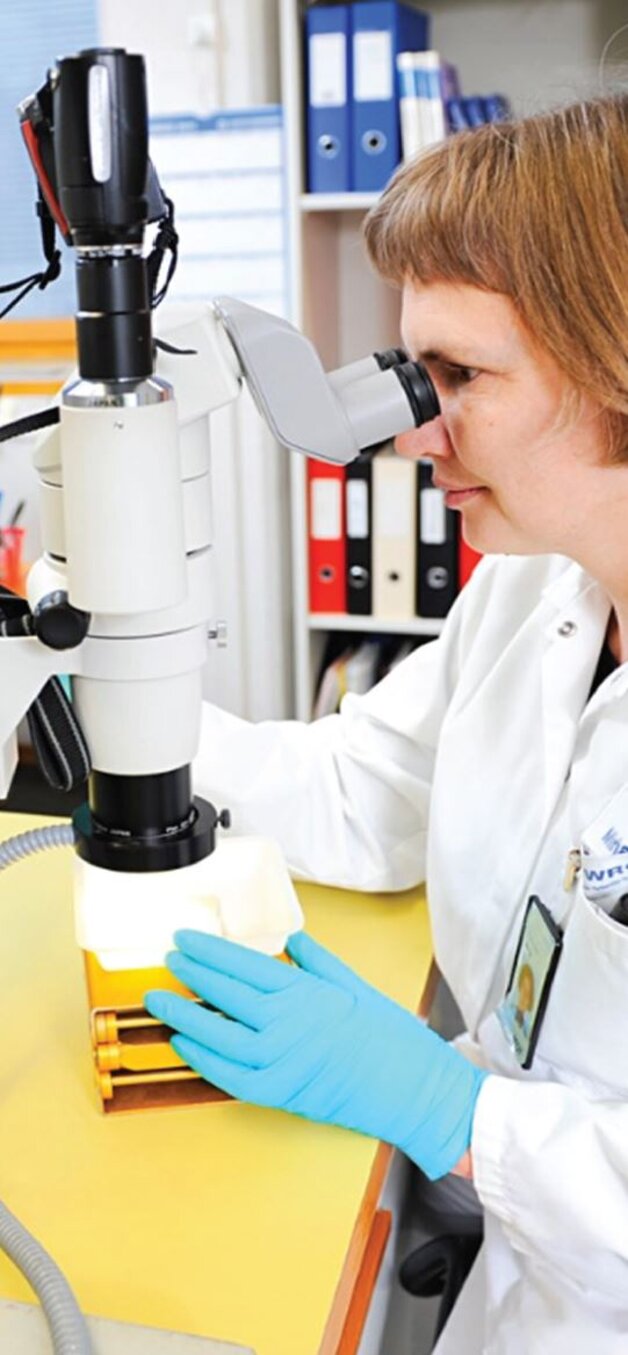