- News and Events
- News
- 2023.03, The Dinex Mixer
THE DINEX MIXER
a unifying backbone in aftertreatment systems
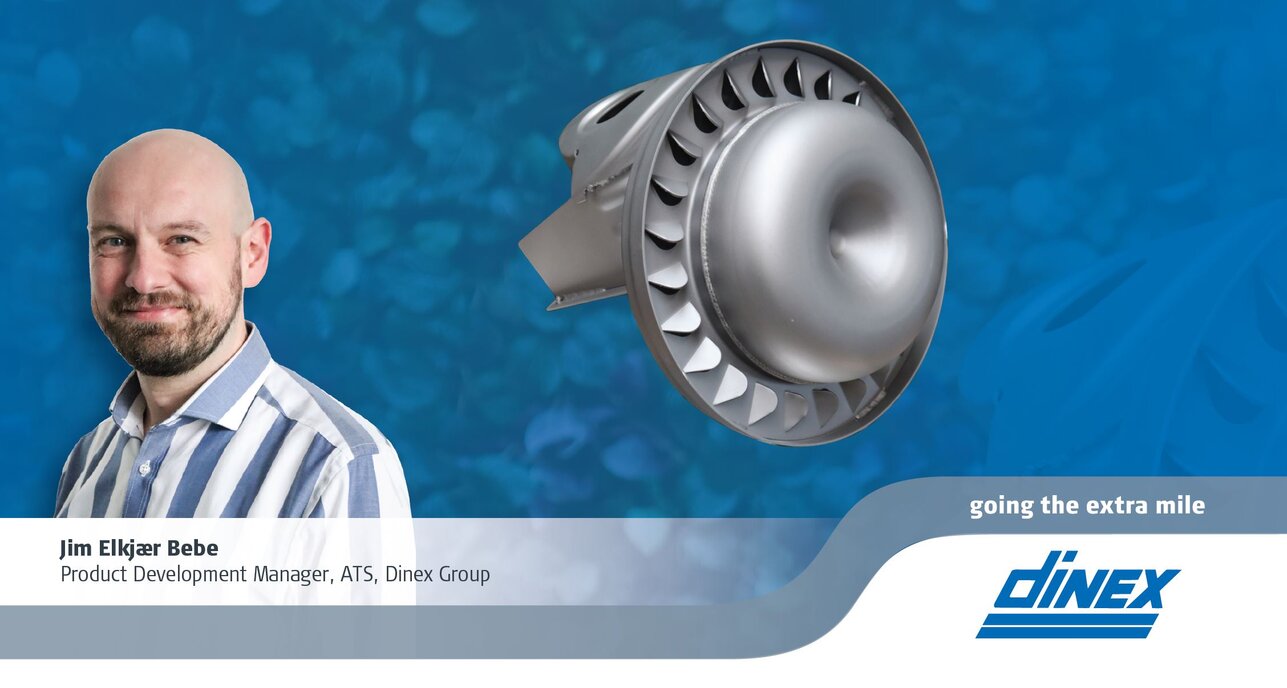
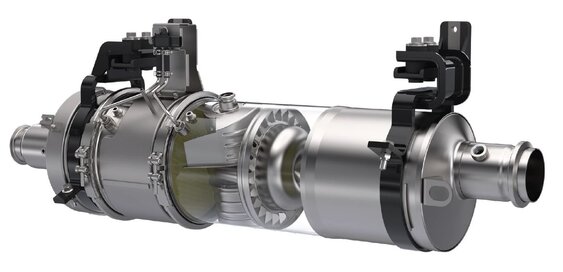
Diesel exhaust gas aftertreatment has come a long way since the 1990s. Regulation has grown more stringent and alongside, public awareness has also increased. The advances in the field of emissions treatment are a benefit to both the environment as well as to public health. But it comes with a price: Technological complexity.
To achieve the legislative targets for emissions, an aftertreatment system (ATS) for heavy duty diesel applications today consist in general of four individual but interdependent technologies: Diesel Oxidation Catalyst (DOC), Selective Catalytic Reduction (SCR), Diesel Particulate Filter (DPF), and finally an often overlooked, yet very critical component: The AdBlue Mixer.
Additionally, the ATS also host a number of important technical solutions.
Those include features for acoustic attenuation, thermal insulation and heat retention, and mounting systems. For a system integrator, managing the complexity of these many technologies and develop a complete solution that meets all customer expectations while still fitting the space-envelope of the vehicle, is a great challenge. Especially as they often rely on finding consensus between several suppliers.
Dinex sits in a unique position, with inhouse competencies covering everything from catalysts to mixers and mounting systems. With the entire solution ownership placed with a single supplier, the possibilities of customizing individual technologies, and making them work in optimal relation to the rest of the system can be taken to new heights and reduce development lead time significantly.
The engineering and science behind the AdBlue mixer
Key for the performance of a mixer is providing a uniform NH3 distribution on the SCR catalyst inlet face while minimizing the risk of urea deposits. The challenge faced in mixer design can be boiled down to the fact that evaporation and decomposition of AdBlue is time consuming and requires much space and thermal energy. The challenge is also multifaceted as it depends on both the quality of the spray of AdBlue injected, on the thermal energy available, and on the time spent in the gas stream.
The quality of the AdBlue spray can be quantified by the size of the atomized droplets. Smaller is preferable as they are faster to evaporate. The thermal energy in the gas stream is directly related to the temperature of the exhaust gas. It is however possible to influence the effect by either increasing flow velocities around the spray plume, or alternatively dedicated mixer faces can be used as evaporation faces. These two approaches allow us to separate mixers in separate general types; namely Swirl-type and Impact-type. The first for enhanced gas stream evaporation and the second for evaporation of dedicated surfaces. Both types essentially also represent strategies to try to limit the space claim of the mixer.
Both types essentially also represent strategies to try to limit the space claim of the mixer.
The mixer also represents a technology of the ATS where a lot of architectural flexibility can be achieved. The range of Dinex mixer technologies are designed for installation in a range of different architectures, from inline through U-shape to S-shape. The mixers are selected from a range of technologies and they are tailored to the specific application based on
extensive application of in-house developed methodologies for CFD (Computational Fluid Dynamics) and physical testing (engine dyno and/or electric heater and blower system).
The Dinex technology example
The patented, swirl-type inline mixer shown in the lead image was developed for the Euro VI and equivalent legislations, and is a true monument to the speed and agility of Dinex. It proudly features a class-leading mixer technology which was subjected to rigorous deposit testing during development and validation in the Dinex Test Facility and performs very good in a wide range of operating conditions, with a wide range of AdBlue dosing rates. Dinex had a production sample of the mixer on display at the recent IAA 2022 and BAUMA 2022 exhibitions in Hannover and Munich respectively where it garnered a lot of attention. The mixer is customizable to fit different injection systems and modular to accommodate different installations, these traits has led the mixer to find application in non-road applications of current legislation as well as being evaluated for future legislation as well. In essence a unifying backbone.
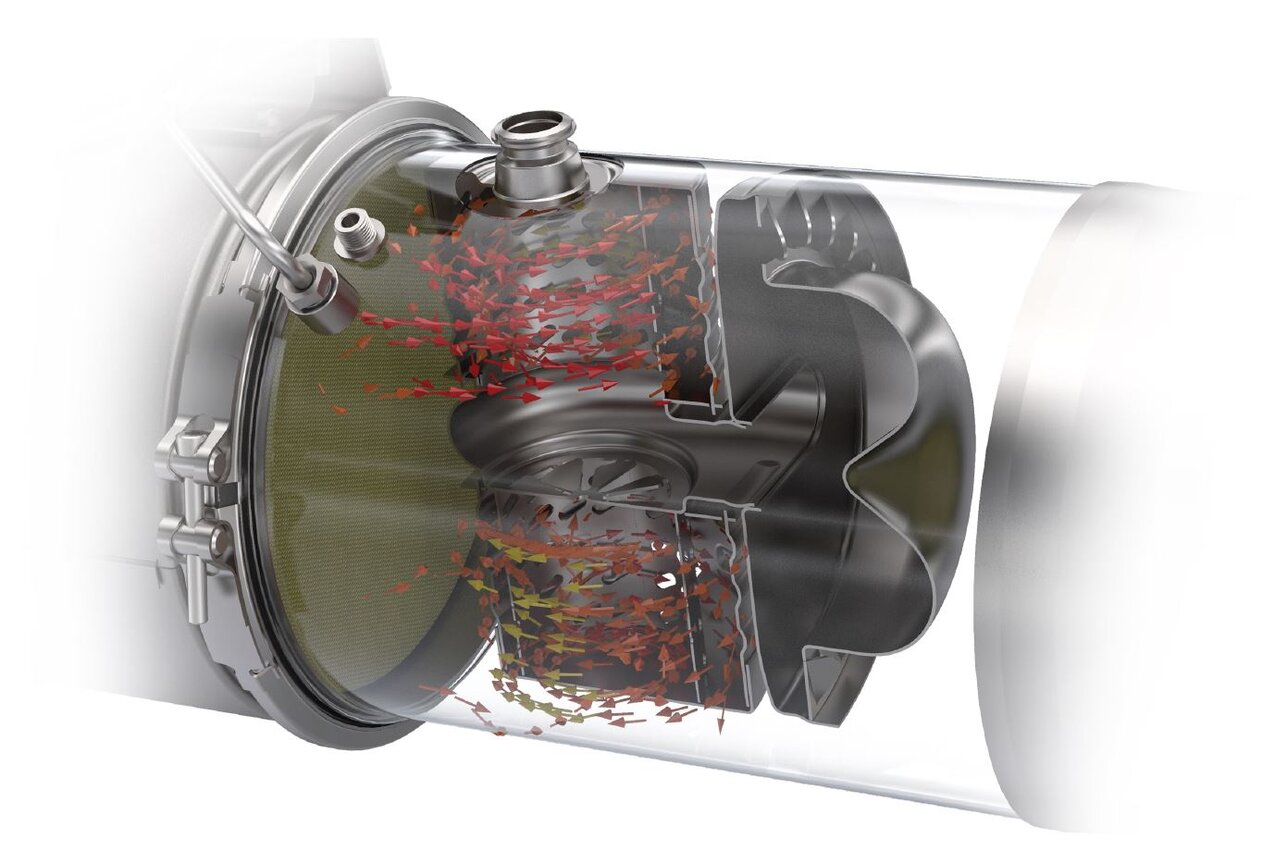
A rendered example of a Dinex mixer technology.
Outlook: An enabler for Euro 7
The (immediate) future of aftertreatment is concerned with tackling the recently published Euro 7 norms. One of the key aspects of this particular emission norm, and by extension also upcoming norms from other region and sectors, is the more stringent NOx targets. A prevalent strategy to achieve the necessary NOx reduction performance is to add an additional AdBlue dosing point, which typically will sit very close to the turbocharger, in a very confined space. Once again demanding ingenuity, creativity and a high degree of customization.
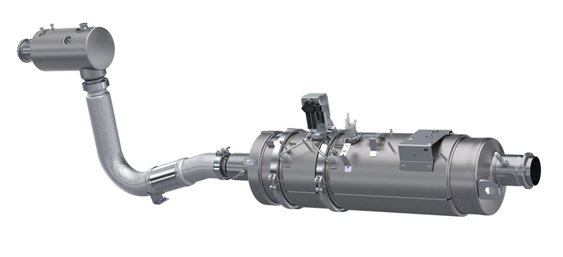
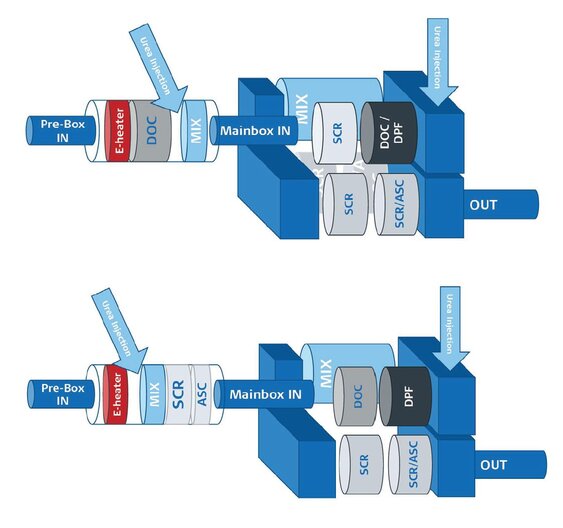
A glimpse of the Dinex OEM Division
Global Footprint - Local Presence
Operating with local teams close to our customers, backed up by global technical competences.
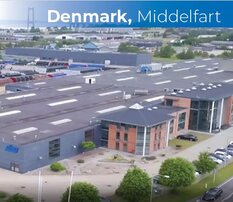
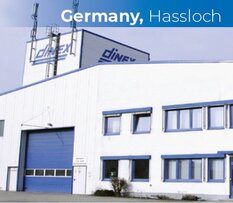
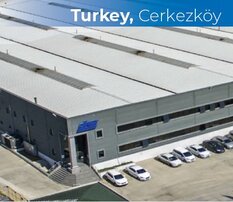
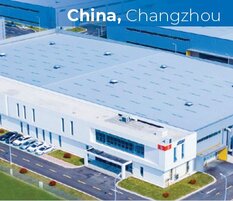
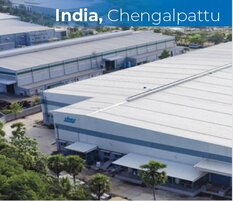
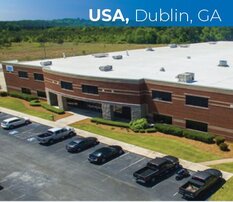
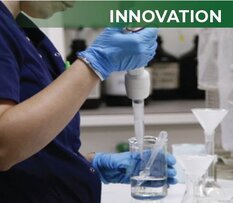
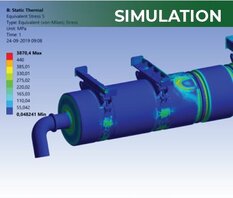
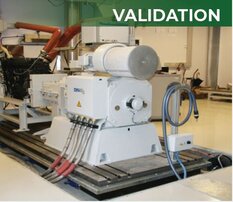
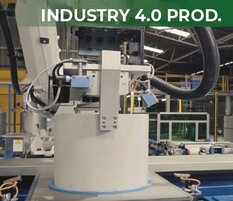
Core Technologies - Proven Solutions
All developed and produced in-house for a simple, cost efficient supply chain with highest solution ownership.
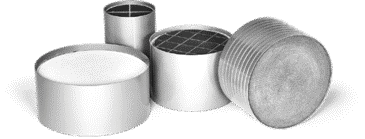
Ceramic and Metallic
Substrates with catalytic coating
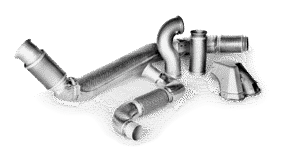
Pipes, Zero-Leakage Decoupling
and Thermal Management
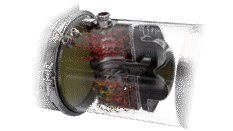
Canning and system integration
with optimal flow and mixing
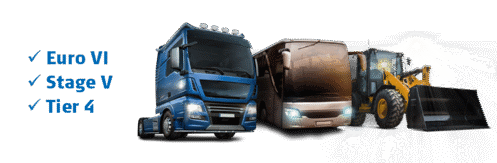
Agile Partnership - Customized Innovations
Full System and customer specific engineering approach: From final application down to coating formula.
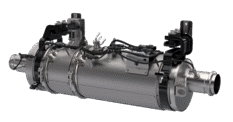
In-line system
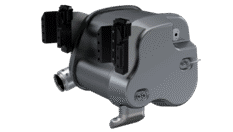
Box system
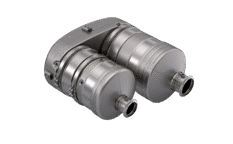
U-Shape system
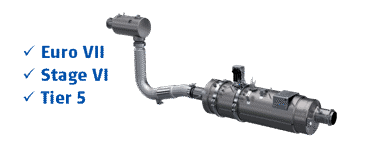
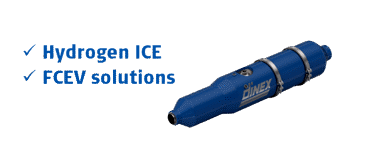